Disruption Or Dissonance? Relativity Space
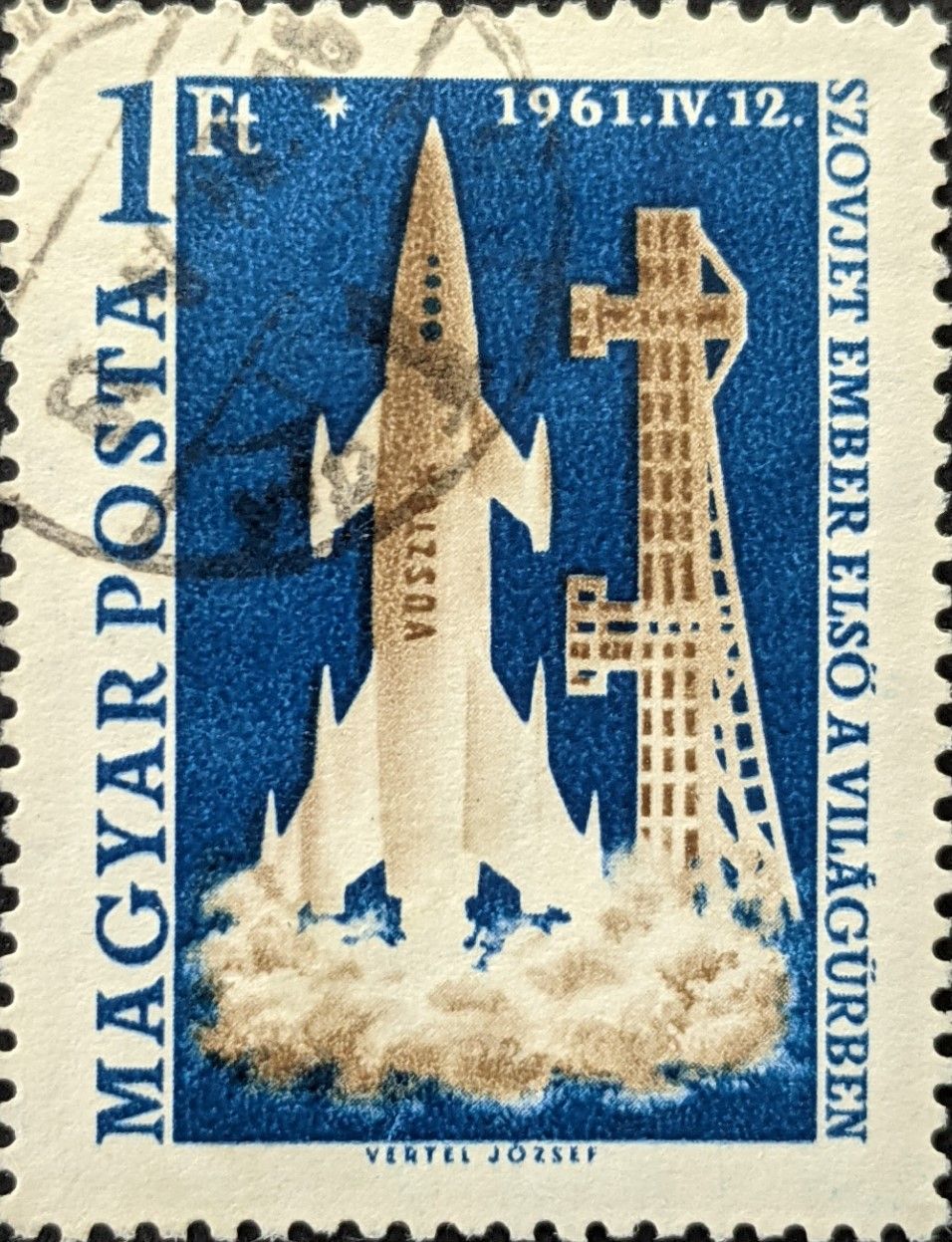
There’s a tendency for some to conflate the new (to the industry) with the groundbreaking and significant in the space industry. That sort of behavior happens more often in the space industry than other tech sectors--at least, it appears that way to me. Part of it may be attributed to the fact the space industry is a confusion of old technology and old processes--anything new is interesting, maybe even threatening. However, part of it is the attempt to entice investors, new and old, to plunk money down for the “next big thing”-usually a technology.
Making a List
Conflation, greed, and confusion are how we have a high-profile “disruptive” company like Relativity Space. Why quote the word disruptive? Because a few days ago, CNBC, the company that routinely covers space companies, awarded Relativity Space number 23 on its Disruptor 50 list. Aside from questioning the propriety of a news organization subjectively awarding companies it is supposedly objectively covering, is Relativity Space the technology disruptor CNBC proclaims in its press release?
That requires looking at Relativity’s claim to fame: 3D printed rockets.
3D printing certainly fits into what the space industry folks believe is needed to change the industry--a new, shiny technology. But is it really that new or shiny? The first patent for 3D printing was awarded in 1980. Based on its 40-year+ history then, the technology isn’t new or shiny. Even the company’s CEO, Tim Ellis, notes this in the CNBC-sponsored press release:
"While Relativity has invented our own 3D-printers ... that's not the most innovative thing, actually…”
What else could be disruptive about Relativity Space? According to CNBC, the most important selection criteria were:
- Scalability
- User growth
- Use of breakthrough technologies (artificial intelligence and machine learning)
- Size of the industry being disrupted
I’ve already established that 3d printing isn’t the breakthrough. Do the other criteria apply? The worldwide rocket manufacturing and launch industry are small, so that surely isn’t a valid criterion to apply to Relativity. Are scalability and user growth applicable? It depends: is Relativity a rocket manufacturing company or just a technology looking for a home? Ellis provided this insight to CNBC, which may help answer those questions:
"We're reinventing the underpinnings of not just building rockets, but the whole stack of how you actually design, develop, build and scale a company," Ellis said.
The 3D-Print Factory for 3D-Print Factories
Relativity Space, then, isn’t “just building rockets.” Ellis makes it sound as if Relativity Space is, instead, a business consulting company (??). Is he attempting to equate the technology his company uses, 3D-printing, as the template for how companies run themselves? Ellis uses the word “scale” but never explains how the scale works in his context. Is this Relativity’s attempt at moving away from building rockets to something else?
Maybe.
Further in the press release, Ellis says this:
"You're telling your customer: 'Go throw away all of your existing factory, all of your existing designs and development, let go of half your team and hire a new team that understands how to build a 3D-printing factory,'" Ellis said.
While Ellis doesn’t come out and say it in the release, he is sticking to another plan in which Relativity will be in the business of building 3D printing factories. This is confirmed in an earlier interview when Ellis also mentioned the desire to send 3D print factories to Mars:
“Once we prove out the factory with this first launch vehicle, we’re convinced this works towards our long term plan of launching factories to Mars and building a wide range of products that you’re going to need there. It’s on the path for the long term vision but also a way for us to be a pioneer in this new value chain for aerospace.”
What we have are at least four public plans for Relativity. The first two are somewhat related--build a rocket with 3D printers. Show the rocket works (a big assumption), then upsell the 3D printer facilities that made it (make bank from NASA contracts for 3D printers to be sent to Mars). The third--reinventing the “whole stack” of a company’s operations seems arrogant at best. Relativity announced the fourth plan in February 2021--build a bigger rocket, too.
However, the upshot is that these diversions from Relativity’s initial rocket-building plans do not provide positive signals about the company’s future. Either that or Relativity really needs to work on its communications skills. I’d be pleased if it was the latter, but I’m more inclined to believe the former.
Relativity’s plans and technology still don’t appear to meet CNBC’s most important criteria for a disruptive company. While the company has tested a rocket engine (several times now), there is not a single finished rocket in evidence from Relativity--odd for a company with in-house access to a rapid prototyping technology (3D printing) for the past six years or so. The company has noted it intends to test its rocket stages sometime in 2021. Those would be significant tests. More significant would be how the company responds to the tests. Will it quickly re-design and then test the prototypes? Or will it take a year to produce the prototypes?
The lack of manufactured rockets may explain Relativity’s interest as a 3D print factory supplier. Relativity has lovely pictures and videos of its factory floors (one of them about 120,000 square feet). They remind me of Virgin Galactic’s operations and training spaces. There are even a few videos of 3D printers creating cylinders. Still, it would be prudent for potential customers to have Relativity display concretely that its factories can produce a complex machine--like a rocket--in one go.
Even then, Relativity’s technology and processes might be too slow.
The Tool is Only as Disruptive as the Company
Ellis has stated his 3D printers “will eventually” create an entire rocket in 60 days.
“Not only will we be able to build a rocket in 60 days, but 60 days later we’ll be able to do a better version. And each version we make, we’ll optimize the mass to make it lighter and cheaper and faster for us to produce,” Ellis said. “This is a completely rewrite of the value chain and I think that’s why people are kind of missing it – they’re looking at it as a manufacturing technology. But it’s really an entirely new way to build, design, and develop a product that’s driven by software.”
To me, this means the company’s factories are currently building rockets (if they exist) much more slowly than that. The amazing thing is, 60 days is slow--at least when compared with SpaceX. Using SpaceX’s Starship activities (instead of Falcon 9) seems like a logical apples-to-apples approach, as it and Relativity’s rocket are both in development. SpaceX’s Elon Musk said a year ago that SpaceX would be producing an entire Starship/Super Heavy rocket every 72 HOURS. Imagine the cost savings and iteration pace there. Another operational rocket company, Rocket Lab, is aiming for 7 days to manufacture its Electron, from start to finish.
Also crucial to Musk and SpaceX was the process and philosophy used to reach that manufacturing pace, which are effective. The company is cranking out prototypes quickly--at least faster than every 60 days, but not as fast as every 72 hours. SpaceX has launched several prototypes over the past year, building them in large tents mounted on cargo containers. My observation: SpaceX is not using the newest technology to make headway in creating what will likely be an industry-changing launch system. What is disruptive, in this case, are the processes and feedback loops the company uses religiously.
Like the welders and rollforming machinery SpaceX uses, 3D printing is just a tool. How a company uses those tools is potentially innovative. When used for building rockets, does 3D printing a whole rocket address relevant pain points during manufacturing? Is part count as much of a problem as the company highlights, and if so, have other companies come up with less capital-intensive methods to deal with that problem? What are the trade-offs? Are the components easily repairable, or must they be reprinted and replaced?
What about 3D printing technology itself? Has Relativity done anything to improve the 3D print process and technology? Are the resulting prints extremely reliable (what percentile) and high quality? Are the machines finicky, based on in-house design software and g-code generation requiring highly paid Relativity specialists (it’s happened with milkshake machines)? Reliability is essential because waiting 60 days for parts to print, only to have a critical print failure during that time, increases the time needed to build a rocket. Printing problems are a nuisance on Earth but could become the difference between life and death on Mars.
It’s also not apparent Relativity is using 3D printers for what they do best--custom, unique, functional designs. Relativity uses 3D printing to create rockets with fewer components, integrating what it can in its prints. Certainly, simplification is desirable, but 3D printers lend themselves to so much more creativity in design. In-house 3D printers can accelerate the process of designing, prototyping, and testing new designs, allowing designers, engineers, and others to complete several cycles within hours.
A company doesn’t need to waste metal on the initial designs, using plastic prototypes instead.
Maybe the company can design rockets that are ultra-strong but require less body mass. Instead of using integrated tanks, maybe design a body that can accept loaded propellant tanks quickly. Body-mounted payload bays in the second stage could be designed to make it easy and quick to load satellites into the rocket. When used to their strengths, 3D printers are an excellent and flexible tool for re-thinking what a rocket is, printing it out, and testing it--quickly. This is why Relativity’s Blue Origin-like pacing is puzzling. But then, it’s only been six years.
If the space industry grows and business booms, then rocket designs need to become more thoughtful about not just one customer’s needs but all of them. The less time it takes to integrate payloads, the less money all those customers are losing. But in the press release, Relativity doesn’t appear to be offering any of those solutions. And I’m sure the company would be talking about those solutions in the press release if it had them.
It’s a pity that Relativity’s in lockstep with a legion of other wanna-be smallsat rocket companies with no operational rockets. Even then, its latest claim of a plan reinventing company operations “stacks” is very much out of step and doesn’t make much sense, either. The good news is that many space companies already have 3D printing somewhere in their workflows. 3D printing is a tool, and the more they use it, the more opportunities they have for figuring out the best way to apply it. They will become familiar enough using the technology’s benefits to revolutionize what a rocket is, addressing common customer pain points in the process.
Relativity is relying on its tool for its distinctiveness: it’s using 3D printers to build its rockets, eventually. Somehow, that fact makes it disruptive in the eyes of investors and media, despite no visible rocket, no revolutionary time savings during manufacturing, and no plan for using a 3D printer for anything more than building cylinders with integrated components. Building cylinders and tanks are probably the least complicated parts of a rocket manufacturer’s process.
Based on the CNBC press release, it’s not clear what Relativity is disrupting--or offering. That’s a little troubling.
Comments ()